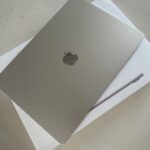
Selection Tips And After-Sales Support Strategies for Highly Adaptable Laptop Shells And Keyboards
22/05/2025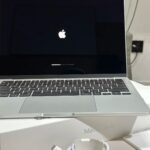
From screen to battery: the full-category quality control system of notebook accessories suppliers
25/05/2025How to reduce operating costs by standardized parts procurement for repair and refurbishment companies
Problems such as scattered accessory procurement, chaotic inventory management, and unstable quality all affect the company’s profits invisibly.
As a professional laptop accessory supplier, we will share three practical standardized accessory procurement strategies and how to help partners achieve cost reduction and efficiency improvement.
- Reasons why standardized procurement reduces costs
- Five cost reduction strategies for standardized accessory procurement
- All-round guarantee solutions from procurement to after-sales
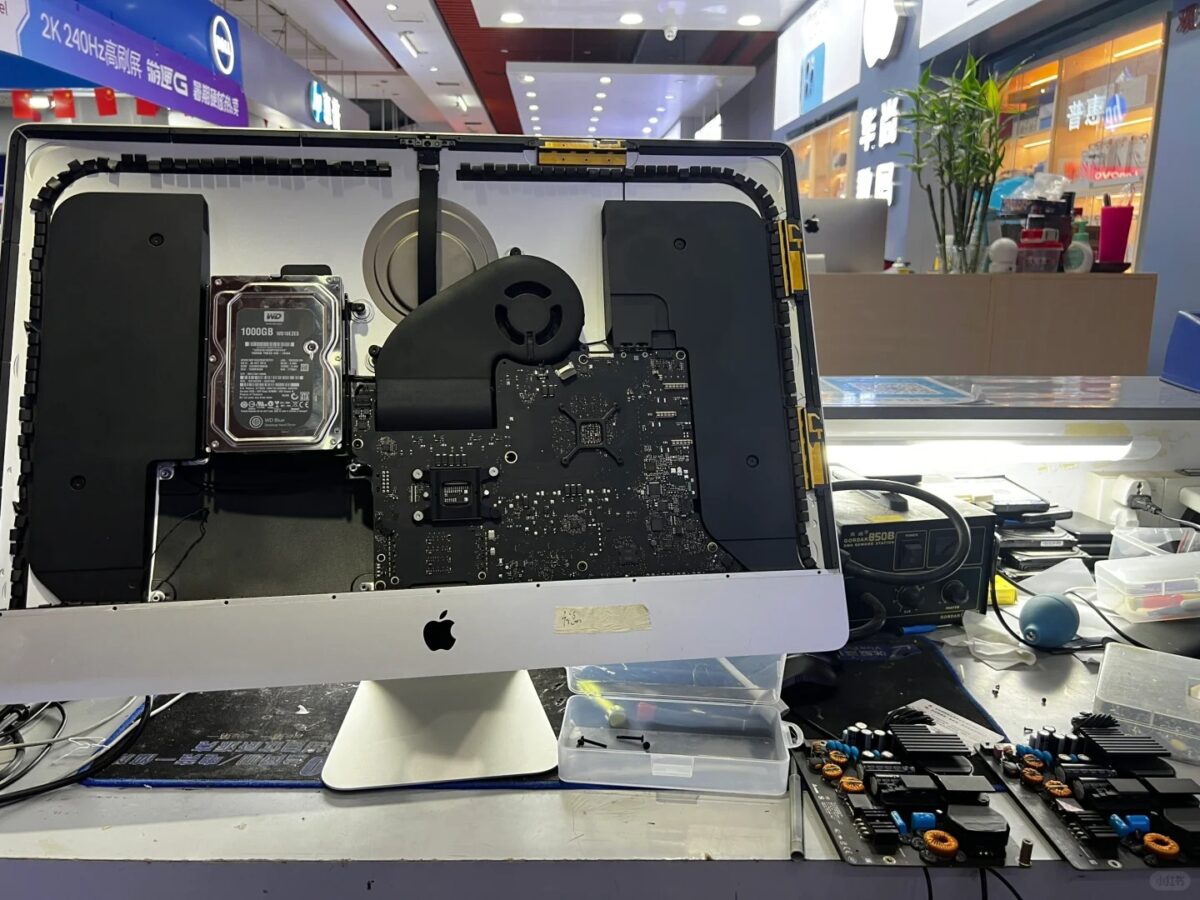
- Why can standardized procurement reduce costs?
Standardized procurement refers to the centralized procurement of accessories that meet unified specifications, quality standards, and certification requirements.
By reducing the diversity of accessory models, companies can achieve economies of scale in procurement, inventory, and maintenance.
According to industry data, companies that adopt standardized procurement can reduce procurement costs and inventory management costs.
- Five cost reduction strategies for standardized accessory procurement
a. Centralized procurement to obtain bulk discounts
Establishing a long-term cooperative relationship with a single supplier and centralized procurement of common components (such as keyboards, batteries, screens, etc.) can significantly reduce unit prices.
For example, after a chain repair company signed an annual framework agreement with us, it reduced the keyboard procurement cost by 15% through quarterly centralized procurement. We provide tiered discounts for bulk purchase customers and open an exclusive price system. The larger the purchase volume, the higher the discount.
b. Streamline SKU and optimize inventory structure
Too many accessory models will lead to inventory backlogs and capital occupation. By analyzing historical maintenance data, we screen out 80% of the core accessories required for the business and streamline SKUs.
We provide inventory data analysis tools to help companies identify high-frequency accessories and recommend safety inventory levels. After a refurbishment company applied this strategy, its inventory turnover rate increased by 40% and its warehousing costs decreased by 22%.
c. Unify quality standards and reduce rework costs
Non-standard accessories may cause compatibility issues and increase the repair rework rate. Our accessories are all certified by international certifications such as CE, FCC, and RoHS, and provide OE (original equivalent) quality assurance.
For example, our laptop screens undergo a 72-hour aging test and color calibration to ensure that there are no bad pixels and color differences after installation, effectively reducing the secondary repair costs caused by accessory quality.
d. Standardize packaging and logistics to reduce distribution costs
Adopt a unified packaging and logistics solution to improve transportation efficiency. We provide modular packaging design to accommodate different types of accessories, and work with international logistics providers such as DHL and FedEx to reduce freight costs through centralized shipments.
A multinational maintenance company reduced its single-ticket shipping costs by 12% through our standardized logistics solutions.
e. Standardized technical support to reduce training costs
We provide unified installation guides, troubleshooting manuals, and online training courses for standardized accessories. Maintenance personnel only need to master a set of standard operating procedures to quickly get started with the installation of accessories from different brands.
For example, our keyboard replacement video tutorial has helped partner companies shorten the training cycle for new employees from 7 days to 2 days.
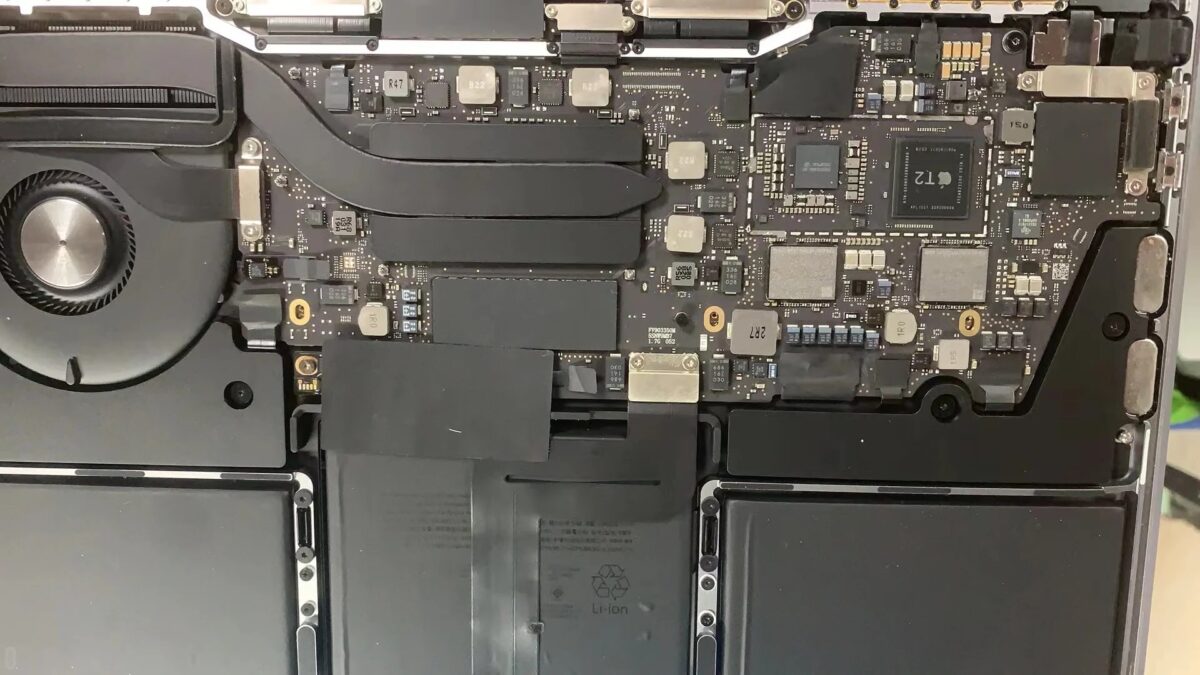
- Our support plan: escort from procurement to after-sales
a.Dedicated account manager: tailor-made procurement solutions for you to optimize the cost structure;
b.Quick response mechanism: expedited orders are shipped within 24 hours to reduce downtime;
c.Quality traceability system: Each accessory has a dedicated QR code to support full-process traceability;
d.Flexible return policy: 30-day unconditional return and exchange to reduce procurement risks.
Standardized accessory procurement is not only a tool to reduce costs, but also the key to improving competitiveness.
It has advantages in quality stability, compatibility and versatility, which can significantly shorten the maintenance cycle, improve conversion efficiency, and thus enhance customer satisfaction.