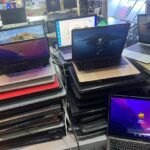
How to reduce operating costs by standardized parts procurement for repair and refurbishment companies
23/05/2025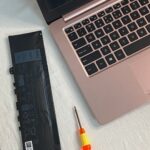
Common Laptop Battery Problems and How Your Repair Business Can Profit from Them
28/05/2025From screen to battery: the full-category quality control system of notebook accessories suppliers
As a supplier of notebook accessories, we are well aware that the quality of accessories directly affects the market reputation of dealers and the service efficiency of repairers.
Today, we will introduce the quality control system of all accessories from screens to batteries, so that you can intuitively understand how we ensure the reliability and compliance of each product.
Strict quality inspection process for core accessories
- Laptop screen: the ultimate control of visual experience
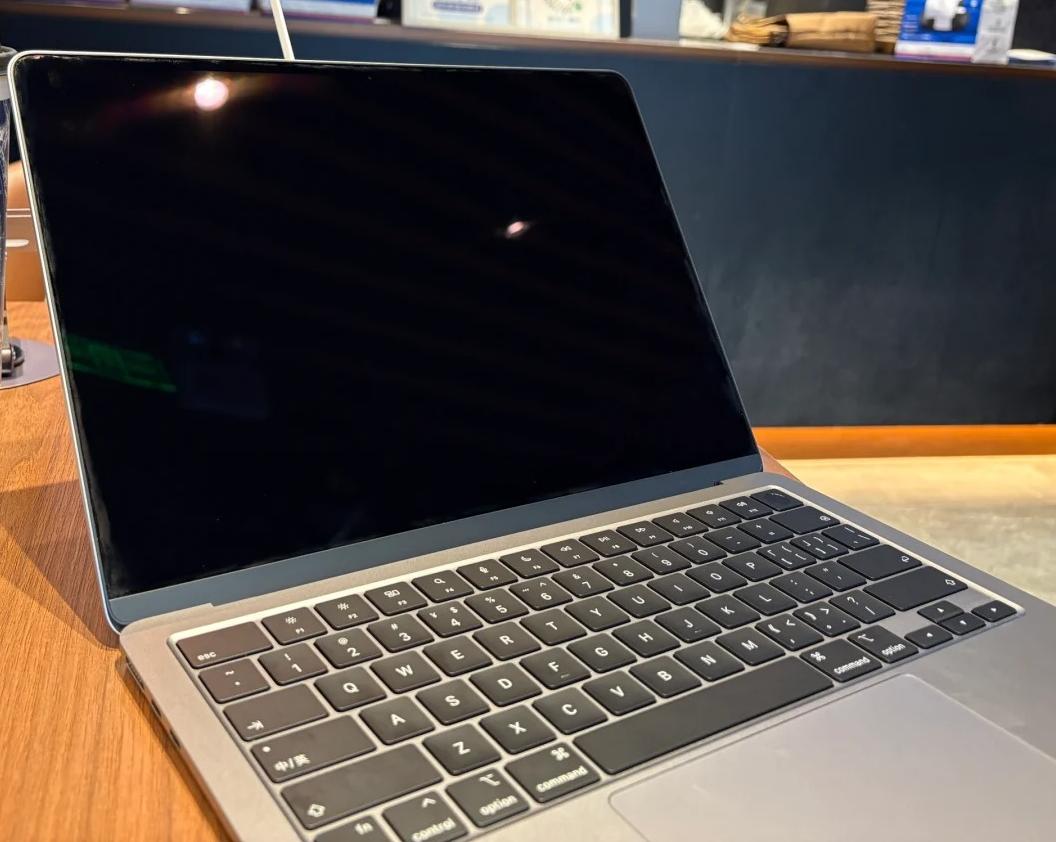
During the screen production process, we implement three-level testing standards.
First, use automated equipment to test the brightness uniformity of each screen to ensure that there is no obvious light spot on the screen;
second, use a professional colorimeter to test the color gamut coverage to ensure that the color reproduction reaches more than 99% of sRGB;
finally, conduct a 72-hour aging test to simulate long-term use scenarios and screen out potential bad pixels, flickering and other problems in advance.
For touch screen products, we will also conduct an additional 100,000 touch pressure tests and waterproof coating adhesion tests to ensure the durability of the screen in daily use. All screen products are accompanied by test reports, which are convenient for you to show quality details to end customers.
- Laptop batteries: dual protection of safety and battery life
Battery safety is critical. Our battery production line is equipped with an AI intelligent monitoring system to monitor the cell voltage, temperature and other data in real time to eliminate the risk of overheating during the production process.
Before each battery leaves the factory, it must pass 20 safety tests such as overcharging, over-discharging, and short circuit, in compliance with international certification standards.
In terms of battery life, we use actual working conditions simulation tests to simulate various usage scenarios such as office and gaming to ensure that the battery capacity reaches more than 98% of the nominal value.
In addition, we also provide a battery cycle life test report. Data shows that our batteries can still maintain more than 80% of their capacity after 500 charge and discharge cycles.
- Other key accessories: The value of quality control performance is demonstrated
Keyboard: After 50 million key life tests, ensure that the rebound force of each key is consistent;
Shell: Use salt spray test to verify corrosion resistance, and pass 1.2 meters high drop test to ensure structural strength;
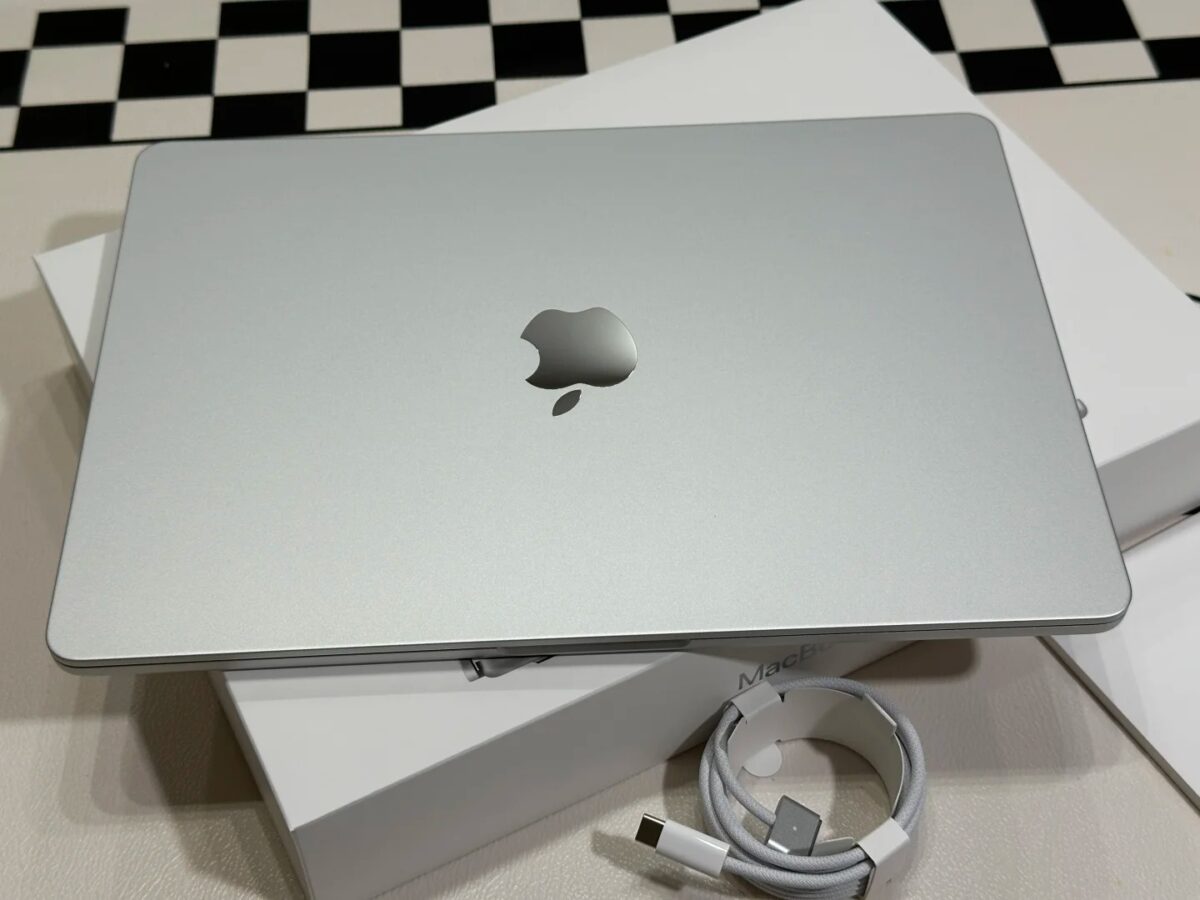
Adapter: Built-in overvoltage protection chip, and pass electromagnetic compatibility (EMC) test to avoid interference with the device.
Three core systems for quality control of all categories
- Supplier management system: control quality from the source
We have established a strict supplier rating system and only cooperate with upstream companies that have passed ISO 9001 certification.
We score suppliers for quality every quarter, and conduct comprehensive assessments from raw material purity, production process to delivery timeliness.
Suppliers with substandard scores will be eliminated to ensure the stability of the supply chain.
- Production process management system: full traceability
During the production process, we introduced MES (manufacturing execution system) to set a unique QR code logo for each product.
From raw material warehousing, assembly, testing to packaging, data from each link is uploaded to the system in real time.
By scanning the code, you can query the product’s production batch, quality inspection personnel, test results and other information to achieve full traceability.
- After-sales quality feedback system: continuous optimization and iteration
We have set up a 24-hour quality feedback channel to collect problems encountered by dealers and repairers in actual use.
We conduct root cause analysis of feedback data every month and optimize production processes or adjust quality inspection standards in a targeted manner.
For example, in response to the problem of loose keyboard interface reported by repairers, we improved the mold accuracy and increased the interface adaptation rate to 99.8%.
Whether you are a dealer or a repairer, we will back you up with reliable quality, transparent control and continuous improvement to help you stand out in the market competition.